Importance of Design for Manufacturability
Design for Manufacturability (DFM) is a critical review process that should be conducted during the early stages of product development (before the tooling and assembly processes). Successful product development relies on design, which serves as the foundation for creating products that meet customer needs, stand out in the marketplace, and are optimized for efficient and cost-effective manufacturing. Here are some DFM principles:
- Making design simpler by reducing product complexity and eliminating unnecessary features. This helps minimize cost and maximize efficiency.
- Making products easier to build by adding self-aligning components or connectors.. This helps avoid errors and simplifies production.
- Standardizing materials and components reduces costs and simplifies manufacturing.
Evolution of Design for Manufacturability
Design for Manufacturability is a modern approach to product development that differs from previous methods..
In the past, designers and electronics manufacturing services providers used their experience and comparable projects as data for manufacturability. Trial and error was the preferred method due to limited production modeling capabilities. It’s obvious that this approach is no longer suitable in today’s fast-changing manufacturing industry, which has led to the development of innovative prototyping solutions like 3D printing.
Designers now have the tools to accurately analyze the connection between design, manufacturing, sustainability, and cost. Robust software tools are now available to them for analyzing and optimizing product design, which reduces errors and costs.
Particulars of the Principles of DFM
Efficient production is ensured by considering several principles of Design for Manufacturability during early product development stages.
Choose appropriate process
The first step is selecting the appropriate manufacturing process for the part or product. Selecting injection molding for a low-volume part may result in high upfront costs due to molds and tooling. Thermoforming could be a cost-effective option as the tooling cost is much cheaper. To optimize product development and manufacturing, it is important to consider production volume, part complexity, and desired features. Longmax deals with a wide range of manufacturing processes.
Design for Efficiency
Efficient, high-quality production requires part drawing and design to comply with sound manufacturing principles. The following example list applies to the plastic injection molding manufacturing process:
- Uniform wall thickness promotes efficient and rapid cooling of the part
- Proper draft angles depends on surface texture
- Avoid thin walls that high injection pressure is needed
- Eliminate undercuts or features requiring side action
- Discussion on design with the contract manufacturer to ensure conformity to sound manufacturing principles
- Ribs should typically be 60 percent of the nominal wall
- Application of the loosest tolerances without functional trade off
Applying the appropriate guidelines should help you avoid potential issues in production.
Pick the right material
Consider the following material properties during DFM:
- Mechanical properties: How strong must the material be?
- Thermal properties: Should the material be heat-resistant?
- Color: Must the part be a specific color?
- Optical properties of the material: reflective or transparent?
- Electrical properties: electronic insulation of the enclosure material?
- Flammability: Does the material need to be flame-resistant? e.g. 94 V-0.
Assess the operating environment
Ensure your part or product is built to meet the production requirement at different operation and storage temperature, drop test, UV exposure and electrical life.
Prioritize compliance and testing
Ensure your product meets safety and quality standards, regardless of whether they are industry-wide, third-party, or company-specific..
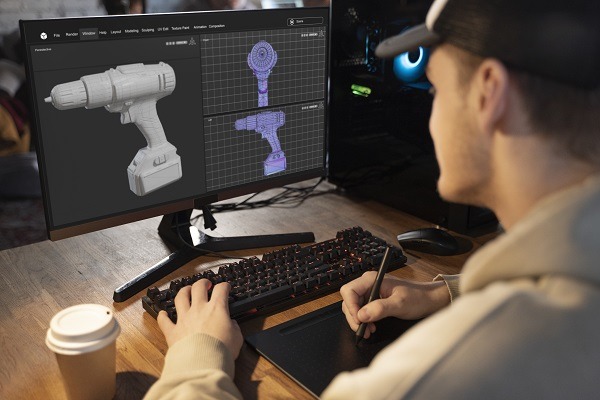
Design for Manufacturability
The importance of Design for Manufacturing
DFM is important for companies to produce products efficiently and profitably, and make crucial decisions in product development.
Considering DFM during the design process can cut production costs and identify inefficiencies.
Effective DFM: Benefits for Buyers of Manufacturing Services
By following DFM principles, product development can result in lower production costs, providing you with benefits.
- Discover and eliminate costly mistakes or design flaws before manufacturing
- Reduce steps in assembly by combining parts
- Shorten time-to-market by increasing product development speed
- Produce higher quality products, components, and parts
- Create a safer working environment by identifying and eliminating potential hazards
How Long Does DFM Take?
The duration of the DFM process is subject to variation, contingent upon the product type and manufacturing process utilized. Typically, the duration for DFM is approximately two weeks, although more complex projects may require an additional week or even longer. The process can be expedited by a product design that is well-defined and in line with the criteria of all parties.
A comprehensive DFM will simplify the design and meet the customer’s requirements for price, specifications, materials, and scheduling..
Conclusion
Following Design for Manufacturing principles can make products simpler and cheaper. Continual improvement of your product is crucial, even beyond the initial design stage. Once you have identified opportunities for improvement, it is advisable to revisit the initial concept in order to integrate the enhancements. The concept of continuous improvement is a fundamental principle in the design and manufacturing of a product.
Design for manufacturing (DFM) is equally crucial in the effort to decrease the ultimate cost of a product while maintaining its durability, quality, and performance. The principles of DFM may seem simple at first, but their positive effect on enhancing the manufacturing process is invaluable. DFM principles can lead to significant savings, so it’s important to consider them when designing or improving your product!